What are the best practices for lean manufacturing in industrial parks?
- Streamline operations to eliminate or minimize waste
- Use data metric tools to measure performance
- Aim for continuous improvement
Now more than ever, operational efficiency is a determining factor for achieving success in the volatile and fast-paced market. During the COVID-19 pandemic, organizations must avoid inefficient practices to avoid putting further damages on their operations. This is why for this article we have rounded up the best practices for lean manufacturing in industrial parks.
Lean manufacturing is rooted in practices Japanese companies used to create a systematic method to minimize waste and identify what truly adds value for customers. While staying within the margins of productivity and quality, this allows firms to reach organizational efficiency for getting ahead of competitors. As the concept of lean manufacturing has evolved, it has been applied to a wide array of sectors, including industrial parks.
Outside of eliminating waste, organizations have the freedom to define and apply their lean manufacturing principles. Unfortunately, this freedom also leaves a lot of ambiguity and tends to produce costly ineffective practices. Whether you are just starting to adopt a lean approach or you are in the midst of it, we’ve put together three proven best practices to follow for implementation in industrial parks.
Streamline Operations To Eliminate or Minimize Waste
At its core, lean manufacturing aims to identify wastes in business processes and eliminate them. If your goal is to deliver as much value to our customers as much as possible, then you have to streamline operations. The more waste eliminated in industrial parks, the more the facilities increase productivity and value. There are a myriad of ways to eliminate waste in industrial parks.
Potential origins of waste in industrial parks include defective products, assembly line bottlenecks, overproduction, inventory shortages, production idle time, equipment breakdowns, not utilizing employee talents properly, logistic errors, lacking process automation where needed, unnecessary bending and reaching for equipment function, spreading workstations that increase travel time among employees, and many more.
Waste in industrial parks can occur at any point in operations — whether from material procurement, production, logistics, to end-customer order fulfillment. It can occur at any point in operations. While it’s impossible to completely eliminate waste, taking proactive actions to minimize them will cause your processes to continually improve and increase your efficiency.
Use Data Metric Tools To Measure Performance
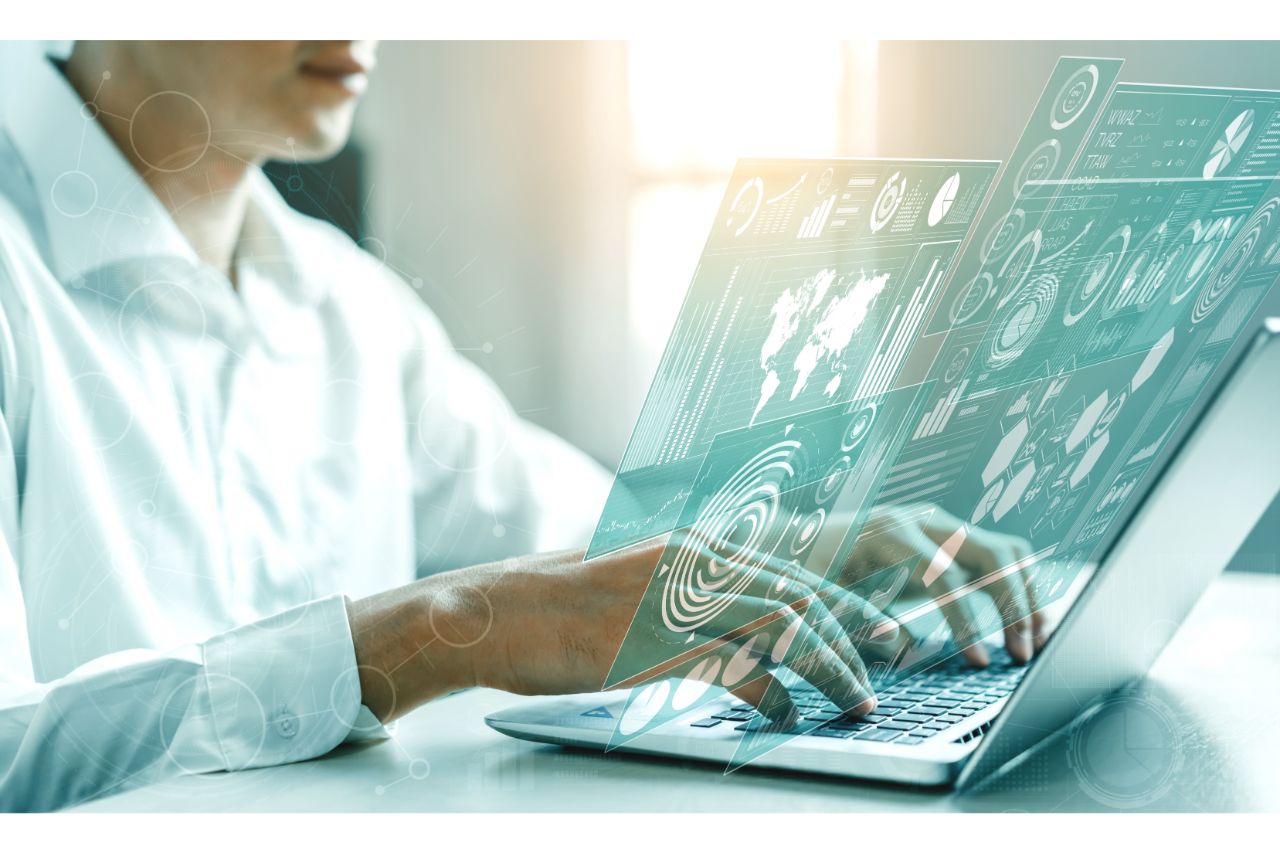
Industrial parks that implement lean manufacturing are committing to improving operations through more efficient processes, which can only lead to further delighting clients. However, establishing lean manufacturing techniques based on its key principles will not be successful without measurement. You cannot improve what you cannot measure.
If you decide to practice lean manufacturing in an industrial park, track the metrics to determine your progress. Thanks to developments in technology, there are many data metric tools that measure lean manufacturing performance. Doing so not only tracks progress but also identifies bottlenecks that were otherwise overlooked. The more tracking you do, the better the odds in preventing costly damages.
Aim For Continuous Improvement
One of the most important fundamentals of lean manufacturing is the culture that encourages continuous improvement. Striving to seek out new and better ways to accomplish industrial tasks can vary from short-term fixes to long-term policies. This can involve rearranging how tasks are completed or retiring old inefficient processes and replacing them with new processes.
Continuous improvement can also happen over a longer period of time through the Japanese term “kaizen”. As a philosophy, kaizen helps discover problematic processes as well as possible solutions. This can range from something as simple as using different carts to store tools and equipment in workstations for faster assembly to reorganizing the entire assembly line to eliminate waste without compromising product quality.
In industrial parks, there are numerous avenues for continuous improvement. For example, investing in independent and sustainable energy grids can prove to be advantageous over blackouts that temporarily disrupt operations. Another example would be investing in employee transportation services to save time and increase operational productivity.
Key Takeaway
In this article, we have rounded up the best practices for lean manufacturing in industrial parks. As you can see, efficiency is the core factor when applying lean manufacturing principles to make sure that everything you do provides value to the end goal.
At Science Park of the Philippines (SPPI), we can help your business apply lean manufacturing techniques to improve operations. With years of expertise, our industrial parks and eco-industrial parks are inclined to help locators minimize waste and attain long-term goals.
Click here to know about what SPPI can offer your company today.